Meta Description:
Discover how modern spreading and rolling systems improve speed, reduce waste, and boost textile production efficiency.
Introduction
In textile manufacturing, production efficiency is vital. Therefore, every second lost during fabric handling can significantly affect output and profitability. To address these challenges, automated spreading and rolling systems have been introduced across modern production lines. Moreover, they streamline the process, ensure consistent fabric quality, reduce material waste, and lessen operator fatigue. Consequently, incorporating these systems can lead to improved overall productivity and cost savings.
This blog explains how these systems work and why they are essential for any textile operation that prioritizes speed, accuracy, and productivity.
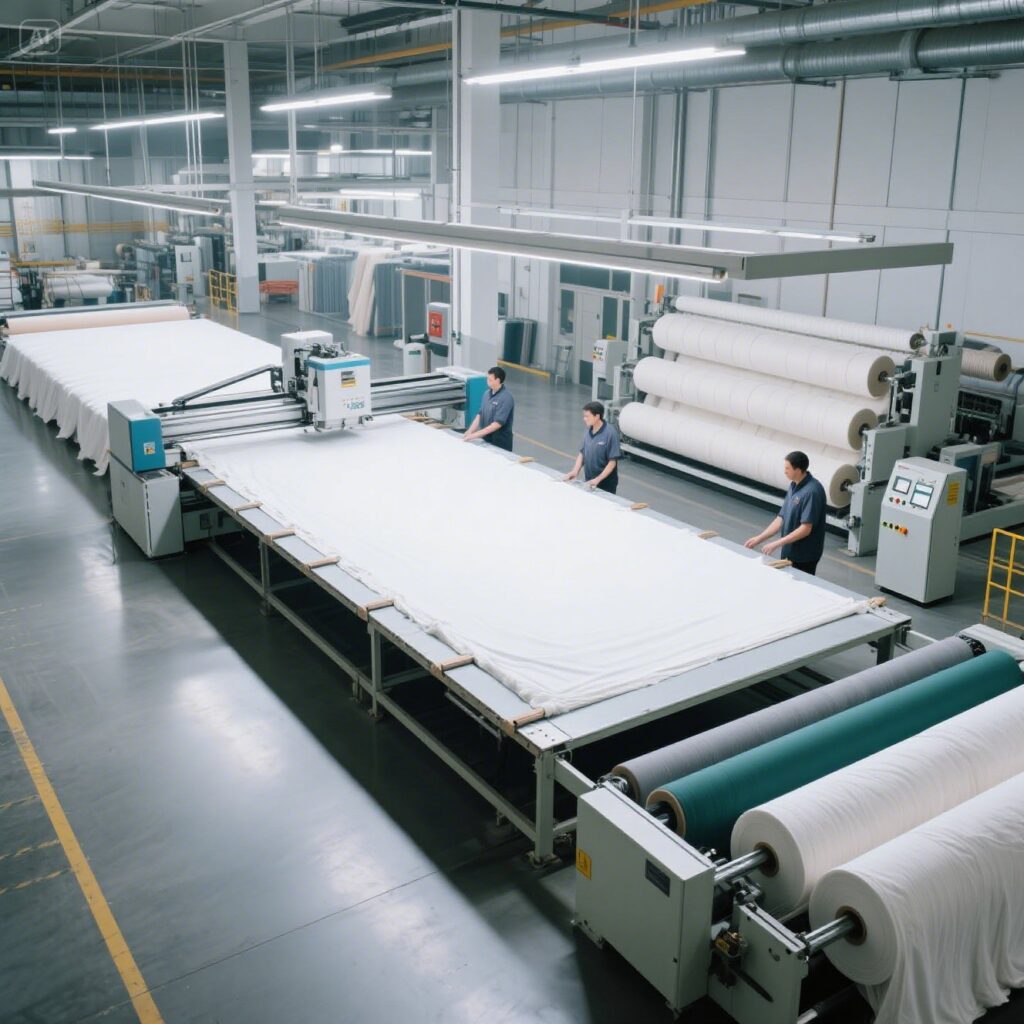
1. What Are Spreading and Rolling Systems?
Spreading systems are machines that automatically unroll and lay fabric onto cutting tables in uniform layers. On the other hand, rolling systems rewind or roll fabric after processing, keeping it aligned and wrinkle-free.
Moreover, you can adjust spreading and rolling for different fabric types, ranging from delicate silks to heavy industrial textiles, ensuring flexibility across operations.
2. Increased Fabric Handling Speed
When done manually, fabric spreading is slow, inconsistent, and prone to human error. By contrast, automated systems can lay down fabric in a fraction of the time.
As a result, more fabric can be processed per hour, leading to greater production volumes without additional labor.
This efficiency translates into faster order fulfillment, a crucial factor in today’s fast-paced garment and textile markets.
3. Consistency Reduces Material Waste
Every inch of wasted fabric reduces profitability.With spreading systems, operators regulate tension, align edges precisely, and minimize wrinkles.
Consequently, they optimize cutting patterns and improve fabric usage efficiency.
Studies show that companies using automated spreading systems experience significantly lower scrap rates than those relying on manual methods.
4. Less Physical Strain on Operators
In traditional setups, workers manually pull and align heavy rolls of fabric. Over time, this leads to fatigue, injuries, and inconsistent work.
Thanks to automated spreading systems, the physical workload is minimized.
In addition, many systems come with ergonomic designs and programmable features, further improving operator comfort and safety.
5. Easy Integration with Cutting Operations
A major benefit of rolling and spreading systems is how easily they integrate with automatic fabric cutting machines. Fabric is delivered in precise stacks or rolls, ready for immediate processing.
Therefore, machine downtime is minimized, and throughput is maximized.
This synchronization results in faster cycle times, fewer interruptions, and, moreover, an overall boost in productivity. Additionally, it helps maintain process consistency and reduces errors, which further enhances efficiency.
Conclusion
Spreading and rolling systems have revolutionized the way fabrics are handled in textile production. From speed and consistency to waste reduction and operator safety, these tools are essential for businesses looking to scale efficiently.
By automating repetitive and labor-intensive tasks, manufacturers can achieve better results with less effort making production lines smarter, safer, and faster.